If you manage a business, chances are that you’ve come across the terms 'SOP' and 'Work Instructions'. While these documents are very similar in nature, they have significant differences in terms of their scope and purpose. Both play a key role in ensuring consistency and success within business operations, making them a vital part of any quality management system.
However, it can be difficult to determine the best way to use these documents and where to implement them in your business model. It is important that you have a thorough understanding of SOPs and Work Instructions in order to meet the regulations outlined in ISO 9001: 2015.
In this guide, we will discuss the differences and benefits of using SOPs and Work Instructions within your business. We provide detailed definitions of SOPs and Work Instructions to help you elevate your business operations and also detail when they should be used and which would be more beneficial.
Read on for a detailed explanation of SOPs and Work Instructions and how they can take your business to the next level.
What is an SOP (Standard Operating Procedure)?
A Standard Operating Procedure, often abbreviated to SOP, functions as a guideline for a variety of different business operations. A SOP document outlines what is to be done and by whom in alignment with your company workflows. To break it down in its simplest form, an SOP should focus on ‘what’ is being done and ‘why’ it should be done. Learn how to write an SOP.
It is important that your SOP provides a general framework for actions to be taken in specific scenarios. It is essentially an overview of how processes are executed and doesn’t delve into specifics. Each task in the procedure can then be broken down into smaller steps and these will become Work Instructions.
A SOP addresses all those involved within the outlined process, allowing everyone to be aligned when it comes to executing operations. They are typically produced by higher-level management and are then distributed to the entire company as a means of providing consistency.
There are a range of Standard Operating Procedure templates online to help you get started and you can find more information about how to write an SOP here.
The benefits of SOPs
A robust SOP is crucial for ensuring that your business is successful and comes with a variety of benefits. From keeping your processes consistent to aiding with employee onboarding, here are some of the ways that a SOP can help improve your business outcomes.
Consistency & compliance
Creating Standard Operating Procedures ensures that you have consistent processes across your business and teams. This consistency is crucial for maintaining the quality of your services and will vastly improve your customer's experience.
Likewise, SOPs can help you adhere to industry regulations and best practices. This helps you avoid any legal issues and ensures the safety of both your staff and future customers.
Training & onboarding
One of the major benefits of an SOP is that it can be a useful tool when onboarding new employees into your business. They provide a structured approach to onboarding, giving employees all the information they need. This can help reduce the learning curve and guarantee that they follow established procedures.
Risk management
A SOP is a useful asset when it comes to handling potential risks and emergencies. This is crucial for both your business as well as your potential customers as a SOP can mitigate risks and help you respond effectively to unforeseen events.
Communication & quality control
Another major benefit of a strong SOP is that it can enhance communication across your organisation. It provides a common understanding of the various processes and keeps team members on the same page in regard to how procedures are to be executed.
Moreover, SOPs play a vital role in quality assurance for various aspects of a business. With well-defined standards, you can monitor the quality of your service or product. This allows you to pinpoint areas for improvement and take corrective actions.
What are work instructions?
Work Instructions break down different operations into detailed step-by-step tasks that are required for their execution. They provide practical guidance for completing processes that are outlined in an SOP. Because of this, SOPs and Work Instructions should inform one another as this will ensure that your processes are aligned and uniform.
Work Instructions also include details about the tools, methods, equipment and responsibilities that are required to complete a specific task. This is crucial, especially if the task requires equipment that has certain safety regulations.
While SOPs are more concerned with ‘what’ and ‘why’, Work Instructions should dive into ‘how’ a task is to be completed in accordance with business standards and regulations. When writing Work Instructions, it is important to bear in mind that they should specifically address those directly involved with the completion of the tasks.
It is a good idea to consistently review your Work Instructions to ensure that they are efficient, concise and easy to follow. You may want to consult experienced personnel and new hires to ensure that the Work Instructions are optimal and revise them accordingly.
The benefits of work instructions
Work Instructions have some tremendous benefits when implemented into your existing processes. They allow you to clearly define how tasks are to be performed and can provide insights into improving your efficiency. Here are some of the main benefits of Work Instructions and how they can help your business thrive.
Precision & efficiency
You’ll know by now that Work Instructions provide detailed guidance for specific tasks within a process. This precision results in tasks being completed accurately and reduces the chances of errors occurring. It also allows those undertaking the tasks to be much more efficient, giving them more clarity on their responsibilities and increasing their confidence in their ability.
Training & development
Clear Work Instructions are really helpful when training new hires. It gives them a document to refer back to when completing business tasks and will help turn these operations into ingrained habits. They also facilitate the development of necessary skills by giving clear instructions and expectations for the effective completion of a task.
Documentation of best practices
One of the most important benefits of Work Instructions is that they keep a record of best practices for different tasks in a process. This is vital for ensuring that your actions as a company are consistent with your Standard Operating Procedure. It also provides value by sharing knowledge across your organisation and ensures the preservation of expertise in your staff.
Adaptability & problem solving
Our final benefit of Work Instructions is perhaps the most important. Work Instructions are more adaptable than SOPs and can be changed much more easily. These changes could come from advances in technology or other processes in your business. Work Instructions can be updated more frequently to reflect the most current and efficient ways of completing individual tasks.
Standard operating procedures vs work instructions: what are the main differences?
Now that you have a better understanding of what SOPs and Work Instructions are, it’s time to delve into the differences between them. They may seem very similar and in some cases may even be used alongside one another, but they serve very different functions.
The major differences between SOPs and work instructions are their standing in the business hierarchy, their purpose, the level of detail and their application. We dive deeper into each of these differences below to make sure you can differentiate them.
Place in the business hierarchy
One of the major differences between SOPs and Work Instructions is their position in the hierarchy of the business. SOPs (and SOP software) are often positioned at a higher level in the documentation hierarchy, providing an overarching road map for various processes within a company. Work Instructions are positioned beneath SOPs in this hierarchy, as they provide detailed descriptions of how a task is to be performed within the broader framework of the Standard Operating Procedure.
Purpose
While they both inform how processes are to be carried out, the purpose of an SOP and Work Instructions have some slight differences.
SOPs have a much broader scope and are aimed at providing guidelines for a particular process or business activity, covering an entire process from start to finish. The main purpose of an SOP is to ensure consistency and standardisation across all business processes.
Alternatively, Work Instructions are more specific and convey a detailed process for how tasks should be executed within a company. Their purpose is to provide a step-by-step guide for individual tasks which make up a larger process.
Level of detail
There is also a difference between the level of detail included in an SOP compared to Work Instructions.
SOPs should provide a general overview of a process, which includes the vital steps and guidelines for completion. They tend to be more brief however, an SOP may include a reference to Work Instructions to provide more detailed information.
Work Instructions are much more granular, outlining specific actions and parameters for conducting a particular task. They tend to be more focused on the execution level and will contain more specific information about the necessary tools, actions and equipment that are required for the operation.
Business application
The final difference between SOPs and Work Instructions is their application within a business. SOPs apply to broader processes that encompass multiple tasks or activities which make up the actions of a company. They are designed to ensure consistency across various stages of a process so that all team members are aligned in their way of working.
Conversely, Work Instructions are task-specific and are usually applied to a single operation within a wider process. They provide the necessary details for someone to perform a specific task correctly and give more insight into how to approach challenges and obstacles.
When to use work instructions vs SOPs?
SOPs and Work instructions can be used for a variety of different businesses and are very adaptable. While Work Instructions are typically aimed at on-the-ground or customer-facing workers, they can also help inform the rest of the business on how tasks are completed.
SOPs and Work Instructions can be used to ensure compliance with safety standards, improve customer relationships and create consistency across the entire booking process. Below you can find some examples of where SOPs and Work Instructions can be used in a business.
- Using complex equipment: Work Instructions are more suitable when tasks require the use of specialised equipment. This allows the user to follow a step-by-step process to avoid injury or errors.
- Customer support: having robust Work Instructions for your customer support team will help them troubleshoot and give them a better comprehension of your communication protocols.
- Quality management: to ensure that your product or service is of the highest quality, a comprehensive SOP that covers overarching processes, inspections and tests is the best approach.
- Financial reporting: an SOP can also streamline your processes for recording and reporting financial information. Your SOP should include processes such as data collection, analysis and the creation of financial documents.
- Emergency response: perhaps the most critical application of an SOP is its use in emergency response plans. Providing clear instructions for actions to be taken and who to report to during an emergency will ensure the safety and security of your staff and customers.
SOPs vs Work Instructions: which is more beneficial for your business?
Both SOPs and Work Instructions are beneficial elements for a variety of processes in a business; the key is determining which would be more appropriate for specific tasks in your company. If the processes in your business are much broader and require multiple steps, a SOP will be much more suitable, whereas detailed and specific tasks would benefit from comprehensive Work Instructions.
You should also consider the adaptability of your processes. As previously mentioned, Work Instructions are much more flexible as they can be updated more frequently. If your business experiences regular changes, Work Instructions are a more suitable means of detailing these tasks.
For the best results, both SOPs and Work Instructions should be used in tandem. Ideally, the different stages of your SOP should be broken down into more detailed Work Instructions that provide further context for how the tasks are to be completed.
Ready to create your SOPs and work instructions?
This guide has outlined the differences between SOPs and Work Instructions and hopefully has given you more clarity on these documents. SOPs are the general framework for how processes are completed and why, while Work instructions dive into the details of executing a specific task.
At Touch Stay, our digital guidebooks can be used to create memorable and eye-catching SOPs and Work Instructions that will improve the consistency and efficiency of your business.
Sign up for our free trial and see how you can make dynamic SOPs and Work Instructions that will boost your business outputs!
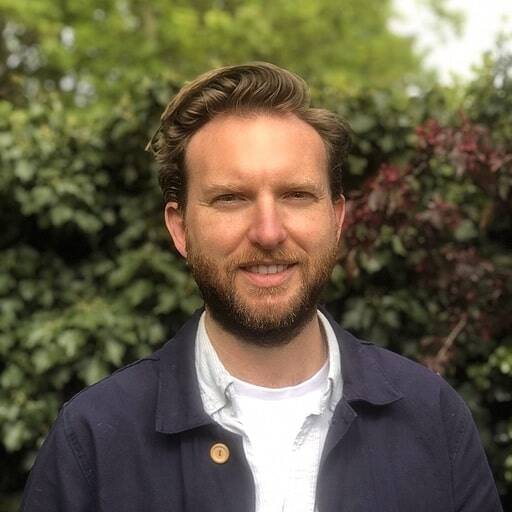
Ned
Ned has clocked up over 11 years in digital marketing and comms, with a strong focus on creating engaging content for a range of brands and agencies. When he’s not writing, he can be found digging for records, peering through his telescope at the night sky, or onboard his local lifeboat where he volunteers as a crewmember.
Be the first to know!
Join our newsletter for early access to:
- ✅ Free guides
- ✅ Pro tips & tricks
- ✅ Time saving tutorials
- ✅ Latest blog posts
- ✅ Checklists & templates